Suspended Magnets, also known as suspended magnets or overhead magnets, are a type of equipment used in industrial processes to separate and remove ferromagnetic impurities from various material streams. It uses the principle of magnetic fields to remove iron and steel impurities from bulk materials during processing or transportation. Under the influence of magnetic forces, suspended magnets can maintain product purity, equipment protection, and the safety and quality of the final product. By placing strong magnets above a conveyor belt or chute, when the material containing ferromagnetic metals passes below, the ferromagnetic impurities are successfully separated and collected from the non-magnetic material.
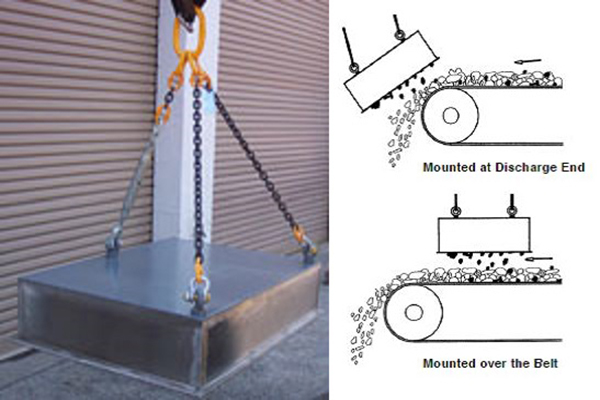
There are three main types:
Permanent suspension magnets – Made up of magnets that work independently without the need for external power, they typically use rare earth magnets with excellent magnetic properties, such as neodymium magnets.
Electromagnetic suspension magnets – A magnetic field is created by passing an electric current through a coil, and the operator can control the magnitude of the magnetic force.
Overhead suspension magnets – Usually mounted above a conveyor belt or material chute, both permanent and electromagnets offer a variety of benefits and are used in a variety of industries.
Suspended Magnets have a wide range of applications
- In the mining and quarrying industries, Suspended Magnets are used to remove metal and mineral impurities from raw materials such as coal, limestone and ore. These magnets protect downstream machinery, such as crushers and conveyor belts, from possible damage and ensure the cleanliness of delivered materials.
- Recycling plants use recycling plant magnets to separate ferrous elements from mixed waste streams. These magnets quickly remove magnetic impurities such as metal fragments, plastics, glass and electronic waste from recyclable materials, resulting in cleaner, higher-grade recyclable materials.
- On construction and demolition sites, construction site magnets are used to efficiently extract ferrous fragments, such as nails and screws, from debris. This process ensures the safety and efficiency of the construction and demolition process and protects downstream equipment, such as crushers and conveyor belts, from potential damage from metal fragments.
- In waste management facilities, waste management magnets are used to sort and separate ferrous fragments from mixed solid waste streams. These magnets aid recycling activities and support more sustainable waste management methods.
- In the food processing industry, food processing magnets are used to find and remove iron impurities in equipment or packaging to maintain the purity and safety of food.
Potential uses and advantages of suspended magnets
The growing demand for suspended magnets in emerging markets, especially in transportation systems such as maglev trains, energy and other fields, provides new market opportunities for suspended magnets. The application of maglev technology in the transportation field can reduce carbon emissions and energy consumption, and future development will focus on innovations in environmental friendliness and energy conservation. Magnetic levitation performance and responsiveness are improved through sensor technology, control algorithms and power electronics technology. Superconducting materials and cryogenic technology can achieve more powerful and efficient maglev systems, thereby increasing the impact of this technology on people's production.