Precast concrete is widely used in modern buildings due to its high efficiency, durability and economy. As a key component for the transportation and installation of precast components, lifting anchors directly affect construction safety and efficiency.
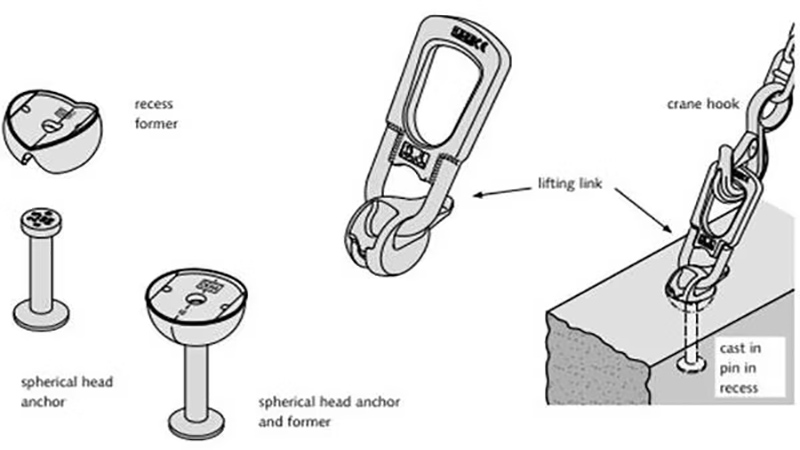
What are precast concrete lifting anchors?
Lifting anchors are pre-buried or post-installed load-bearing components used to lift and install precast concrete components (such as wall panels, beams, columns, composite slabs, etc.). It must have sufficient strength to withstand dynamic loads during lifting, transportation and installation.
Main types of lifting anchors
1. Pre-embedded anchors: embedded before concrete pouring
- Lifting Loops – suitable for vertical lifting (such as wall panels, stairs).
- Threaded Inserts – can be connected to the lifting anchor by bolts after the concrete hardens.
- Plate Anchors – used for heavy components (such as beams and columns).
2. Post-installed anchors: installed after the concrete hardens
- Bolt-on Anchors – fixed by high-strength bolts.
- Undercut Anchors – provide high pull-out resistance.
3. Special anchors
- Swivel Anchors – allow angle adjustment during lifting.
- Lifting Clutches – suitable for double T-slabs and hollow slabs.
Key design points
1. Load calculation
- To consider:
- Static load (self-weight of component)
- Dynamic load (hoisting impact, usually calculated as 2 times of static load)
- Safety factor (generally ≥3, in accordance with EN 1992-4 or ACI 318)
2. Anchor arrangement
- Should be located at the center of gravity of the component to avoid tilting.
- Multiple anchors need to be evenly stressed to prevent local overload.
3. Concrete strength - The anchor depth must meet the pull-out requirements.
- The concrete strength during hoisting must reach the design value (usually ≥20MPa).
4. Anti-corrosion treatment
- For outdoor or corrosive environments, hot-dip galvanized or stainless steel anchors should be used.
Installation specifications and precautions
1. Construction according to specifications - strictly follow the burial depth and spacing requirements provided by the manufacturer.
2. Inspection before lifting - confirm that the anchor is free of cracks, deformation or rust.
3. Matching lifting equipment - the rated load of the sling and shackle must be greater than the weight of the component.
4. Smooth lifting - avoid sudden acceleration or sudden stop to reduce impact force.
5. Post-processing - exposed anchors need to be removed or protected from rust.