In the contemporary construction sector, prefabricated formwork has gained widespread adoption across residential, commercial, public buildings, and infrastructure projects in Europe and the United States. Specifically, in residential construction, prefabricated formwork is utilized for prefabricated and modular housing. For commercial developments, it is employed in office buildings and shopping malls. In infrastructure, it is integral to bridges, tunnels, roads, and other critical projects. The reliability and safety of precast concrete formwork during construction ensure it meets the stringent standards required by the industry. This raises the question: what are the primary standards governing prefabricated formwork in Europe and the United States?
Firstly, European standards encompass:
EN 12370:2006 - This standard outlines performance requirements and testing methods for precast concrete formwork, addressing the following aspects:
1. Load-bearing capacity: Templates must withstand maximum static loads, including concrete weight, personnel, and equipment. Dynamic load-bearing capacity considers potential vibrations and shocks during construction.
2. Stiffness: Templates should maintain sufficient rigidity to prevent surface defects in concrete due to excessive deformation. Support systems must be designed to provide adequate support under load.
3. Durability: Materials should resist harsh environmental conditions such as moisture and corrosion, allowing for multiple reuses to reduce costs and environmental impact.
4. Safety: Structural stability during installation and use is paramount to prevent collapses from improper support or material failure. Design considerations must prioritize operator safety during assembly and disassembly.
Additionally, Europe adheres to two other key standards:
EN 13369:2006: Specifies performance requirements and test methods for connections and fasteners to ensure overall formwork system stability and reliability.
EN 12371:2006: Provides detailed guidelines for the installation and safe operation of precast concrete formwork.
Secondly, North American standards include:
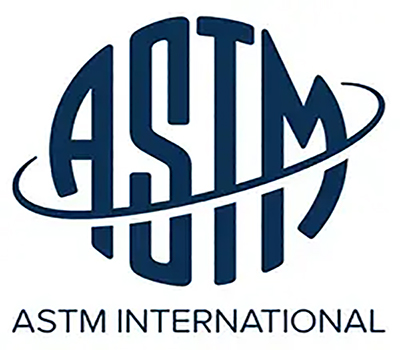
ACI 318-14: Code for Concrete for Building Structures, serving as the foundational code for concrete structure design in the United States. It details technical requirements for concrete structures, including prefabricated components.
1. Material Requirements:
Concrete: Must meet strength, durability, and workability criteria.
Reinforcement: Properties and quality must comply with ASTM standards.
2. Design Requirements:
Load-bearing capacity: Templates must withstand design loads, including self-weight, construction loads, and environmental loads.
Structural analysis: Ensures stability and safety under various load conditions.
Connections and joints: Properly designed to ensure structural continuity and stability.
3. Construction Requirements:
Quality control: Strict adherence to quality control standards ensures installation and fixation meet design specifications.
On-site inspection and testing: Regular inspections verify performance and quality.
4. Durability Requirements:
Durability: Designs must consider long-term use, including corrosion and fatigue resistance.
Protective measures: Prevent damage during construction and use.
PCI Standards:
The Precast/Prestressed Concrete Institute (PCI) develops and maintains comprehensive industry standards covering design, detailing, manufacturing, transportation, and installation. PCI standards are rigorously reviewed and certified by ANSI for broad applicability.
ACI Standard:
ACI 318: Code for Concrete for Building Structures, serves as the foundational code for concrete structure design in the United States, providing detailed technical requirements for concrete structures, including prefabricated components.
International Building Code (IBC):
The IBC, approved by state and local legislatures, adopts relevant standards such as ASCE 7 and ACI 318, providing a legal framework and technical basis for precast concrete applications.